Imagine you have a diverse team of experienced and multi-talented employees ready to put their all into their work.
You’ve got the latest tools and technology at your fingertips.
Best of all, you’ve got an idea for a product that will absolutely blow your audience away — and make everything else in your industry look like child’s play.
You get your team together, tell them what you’re looking to make happen, and give them free rein to do whatever it takes to get there.
…and things quickly fall apart.
The problem?
While your employees know what they’re doing, they approach everything they do without any kind of strategy or gameplan. This not only causes their own efforts to go off the rails — but also leads to massive bottlenecks for the entire team.
In short, they haven’t standardized their processes.
In this article, we’ll dive deep into:
- What it means to standardized your processes
- The benefits and challenges of standardizing processes
- The steps and best practices to follow when standardizing processes
Let’s get started.
What are Standardized Processes?
A standardized process is a clearly-defined approach and workflow that is uniformly applied throughout an organization or industry when performing a specific task.
Most of us have either seen standard processes in action — or are at least familiar with some of the more common examples, such as:
- Assembly line production
- Fast food preparation
- Routine healthcare provision
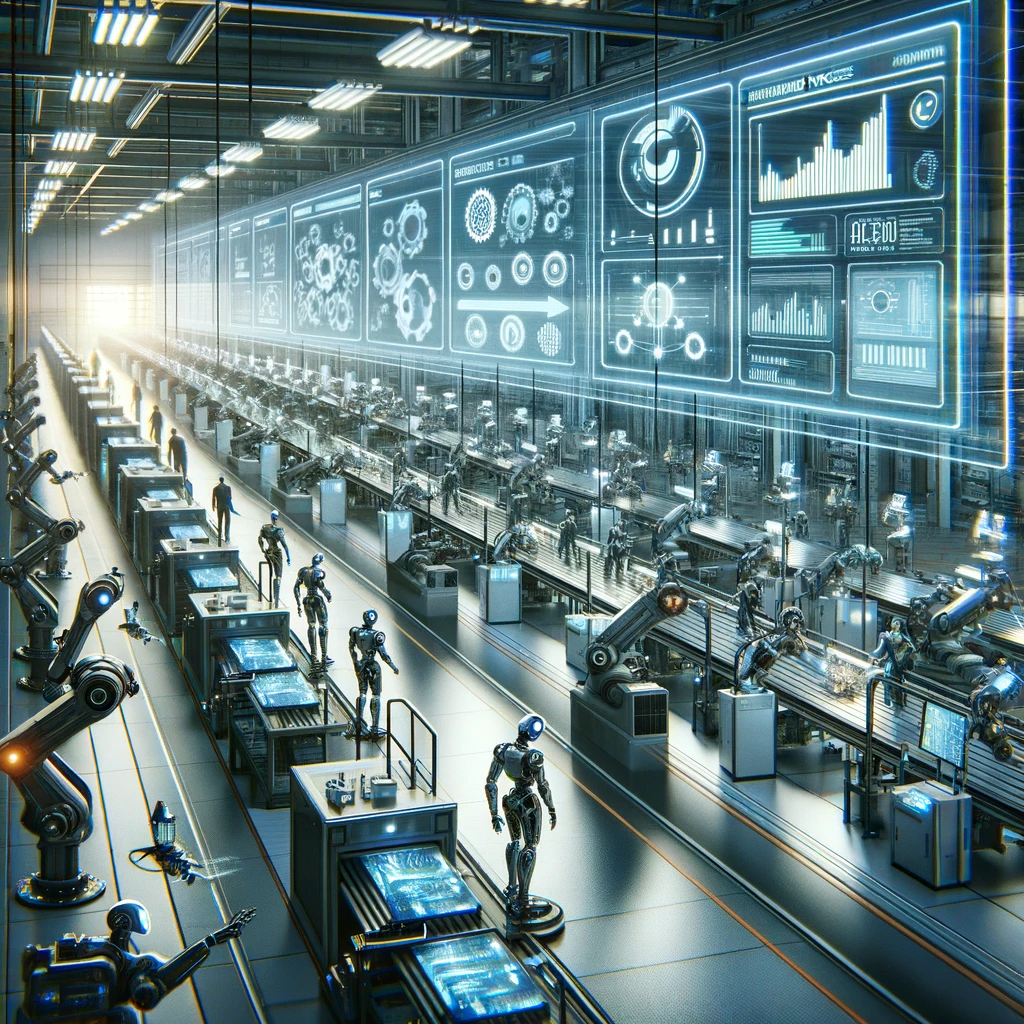
Fittingly, here’s DALL-E’s representation of “standardized process”:
Organizations in all industries often standardize common internal practices, like invoicing, hiring, and employee onboarding.
Now, process standardization is the practice of establishing and implementing a standardized process within your routine business operations.
This involves:
- Defining the standard you’ll be aiming to achieve, both quantitatively and qualitatively
- Creating standard operating procedures and defining best practices to adhere to throughout the process
- Documenting and disseminating the above information to all stakeholders
- Training the appropriate staff members to facilitate the process, maintain quality control, and make ongoing improvements to the process
This more comprehensive process is what we’ll be focusing on in this article.
Benefits of Standardizing Core Processes
On just the surface, it’s pretty clear that establishing standardized processes for routine operations beats a haphazard approach every single time.
Still, it’s worth taking a closer look at how doing so can help your organization both now and in the future.
Create and Deliver Consistent Value
Standardizing your core processes all but ensures you’ll be able to consistently provide top value to your customers moving forward.
(Which, in itself, leads to a number of benefits for your business.)
This goes for your customer-facing and internal processes, too:
In standardizing your customer-facing processes, you guarantee your customers will get what they expect (and more) every time they engage with you. In standardizing your internal processes, you guarantee that the backend prep work is done to allow you to consistently provide for your customers.
Enhance Individual and Team Productivity
On both an individual and team-wide basis, standardizing essential processes will lead to an increase in productivity for your organization.
Individually, your employees will know exactly what’s expected of them when performing routine operations — typically those that don’t require going off-script all that often. With practice, your employees will be able to perform even the most complex tasks with precision and efficiency.
(That said, you absolutely can standardize operations that do require more critical thought and autonomous action from your employees. More on this in a bit.)
As for your team as a whole, the benefit is twofold:
- If each individual is operating to a higher capacity, your overall productivity will increase substantially.
- What’s more, aligning around uniform standards and routines will allow your teams to become more aligned when working together on a project or initiative.
(In many cases, regular communication and collaboration will be built into your standardized processes — galvanizing teamwork into the foundation of your company’s operations in turn.)
Minimize Waste
Minimizing waste is one of the key reasons — and often the key reason — teams choose to standardize processes at all.
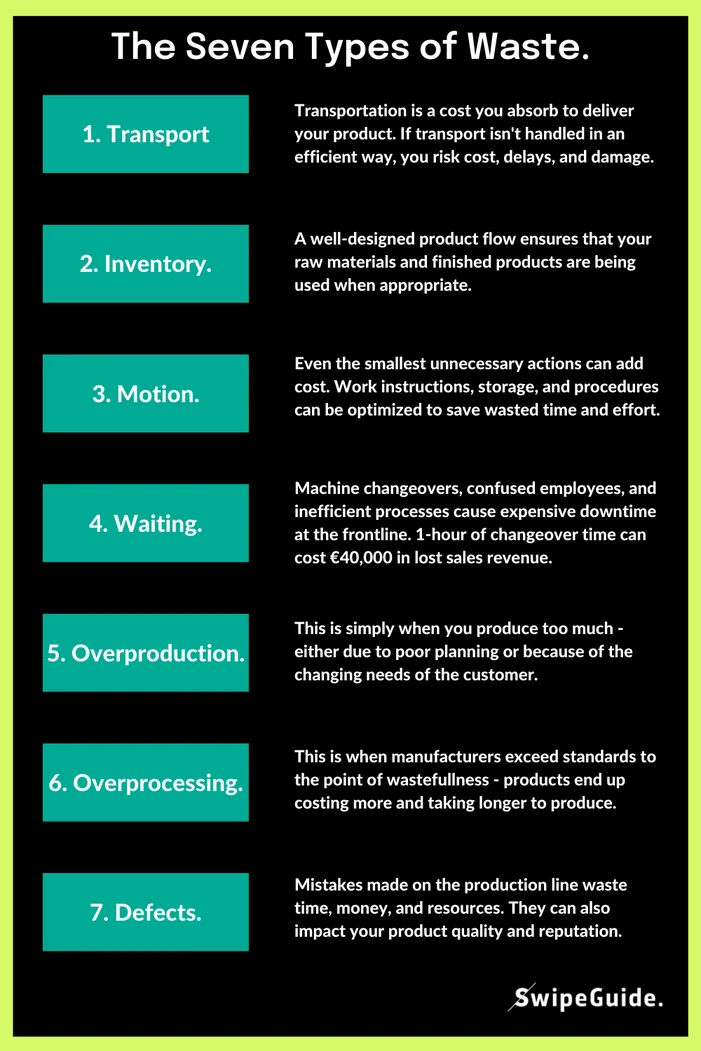
This ties back in with the idea of consistency:
If you always perform a task the exact same way, you’ll always know how much resources you’ll need to complete it. From there, you can plan accordingly to ensure you have enough of what you need — and never end up overspending.
Improve Safety and Compliance
Standardizing certain practices can also be a matter of safety for your personnel — and a matter of legal compliance for your business.
A few examples:
- Creating standardized protocol for dealing with workplace injuries or disasters
- Standardizing customer data intake and storage practices
- Developing training that meets and exceeds industry standards
Even when not legally compelled to do so, standardizing high-risk processes can help your team avoid certain tragedies — and otherwise minimize the damage done when things do go wrong.
Facilitate Ongoing Improvement
Standardizing your core processes is all about figuring out what works best, then doing it on repeat until further notice.
Of course, what works best today might not necessarily work tomorrow — meaning you’ll need to constantly be improving on the best practices you’ve (apparently not) set in stone for your team.
The good news is that creating standardized processes actually sets your team up to make these ongoing improvements simply as a matter of course. As we’ll discuss, building continuous growth into your workflows is a huge part of the equation here.
Moreover, having step-by-step processes in place makes it easier to identify which step(s) to prioritize — as opposed to simply knowing that “something needs to change”.
Key Challenges of Process Standardization
To be sure, standardizing your processes comes with its fair share of challenges.
The first step to overcoming them, though, is knowing what they are — and anticipating them before they cause too big of a problem for your team.
The Investment
There’s no doubt that standardizing even the simplest of processes takes quite a bit of time, money, and other resources.
(Really, it’s a key reason that a strategic approach is so crucial. If you’re just throwing darts at the wall, you’re gonna end up wasting much, much more.)
Implementing a new process will also disrupt your team’s productivity, at least to some degree. Especially in cases where safety and security are concerns, you may need to pause certain operations completely until the new process is in place.
To add to all that, it will likely take some time for your investment to have an impact on your bottom line — if it does at all. In many cases, standardizing your processes is more about avoiding potential costs associated with inefficiencies, non-compliance, and safety breaches than about immediate financial gains.
(Obviously, the initial investment is well worth it in the long run. Still, it can be a tough sell to teams already operating on a shoestring.)
Resistance to Change
If resistance to change wasn’t common amongst employees and teams around the world, change management wouldn’t be a thing.
But it is.
(In fact, 39% of digital transformation efforts fail for this specific reason.)
Even if you have a good handle on implementing change, standardizing too many processes at once or in succession can cause major fatigue for your employees. While optimizing everything as quickly as possible sounds good on paper, you’ll need to space your efforts out to avoid burning out your team.
A Loss of Flexibility
Standardization inherently makes processes more rigid.
It’s…kinda the point.
But standardizing your operations to the point that your employees
- Have no autonomy, and/or
- Don’t know what to do when things go wrong
…is a recipe for disaster.
For one, it can cause your operations to go completely off the rails — and leave you with little wiggle room as to how to deal with it. Worse yet, it can damage the relationship you have with your employees or customers. In worst case scenarios, forcing your team to stick too close to the script can lead to bodily harm for them or your clientele.
We’ll come back to it, but let’s just be clear that there is such a thing as too much standardization.
Maintaining Compliance and Quality Control
Ensuring compliance and quality control throughout the transition to new standardized processes — and maintaining those standards over time — can be challenging for a number of reasons.
For example…
- Employees may struggle with changes from established routines, leading to inconsistent application of the new standards.
- Employees may need additional training and experience to fully adhere to the newly-introduced standards.
- Problems when migrating to new software or other technology can cause you to fall out of compliance.
You’ll also need to be sure that your new way of doing things doesn’t interfere with other areas of operation — especially in cases when legal compliance is a concern.
Essential Steps to Standardizing Processes
Now, let’s walk through the main steps to take when standardizing a given process within your organization.
1. Identify Processes to Standardize
If you’ve just started thinking about this whole standardization thing, the first thing you’ll need to do is identify which of your operations to focus on.
You can start by looking to your industry and niche — and to the internal processes that are universal to businesses in all sectors. From there, you can prioritize which area to focus on based on your current situation.
Some factors to consider here:
- The impact of standardizing — and not standardizing — a certain process
- Your team’s current capacity and ability to make a given change
- The order in which to standardize certain processes
One good rule of thumb here is to focus on processes that apply to multiple areas of your operations. For example, since all departments deal with data entry on some level, standardizing your data entry, storage, and deletion processes should almost certainly be a priority.
In that same vein, be sure to “zoom out” once you identify a potential process to standardize. Again, you might realize there’s a broader, more impactful operation to focus on that will make standardizing this subordinate workflow much easier in the future.
2. Define Your Goal for Standardizing a Process
Next, you’ll need to refine and define your rationale for standardizing the process in question.
Essentially, this means setting qualitative and quantitative goals for the upcoming initiative.For example, if you’re looking to streamline your document management and review processes, you might define your goals as:
- Qualitative: Improve the ease of access and retrieval of documents for all employees, enhancing overall workplace productivity and reducing frustration associated with lost or hard-to-find documents.
- Quantitative: Reduce the time taken to retrieve documents by 40% within six months of implementing the standardized document management system.
Now, you might actually want to hold off on setting quantitative goals if you don’t yet have much data to work with, or if you haven’t mapped out your current processes.
Speaking of that…
3. Map Your Current Process
Even though you’ve yet to fully standardize the process, you likely have a rough idea of how it plays out in practice.
So, you’ll now want to map out the process, as is, to the best of your ability.
In doing so, you’ll be able to identify where things are working well — and where there’s clearly room for improvement. You might also uncover previously overlooked blockers or bottlenecks that end up being a focus for your standardization efforts.
Additionally, you’ll want to determine whether the process looks the same in practice as it does on paper. This can be done by:
- Analyzing employee performance data
- Collecting feedback from team members and stakeholders
- Observing the process in-action
From there, you might now decide to revisit your quantitative goals and paint a more realistic picture of what your efforts can accomplish.
4. Develop and Document the New Process
The next step is to create the new process — and a plan for implementing it.
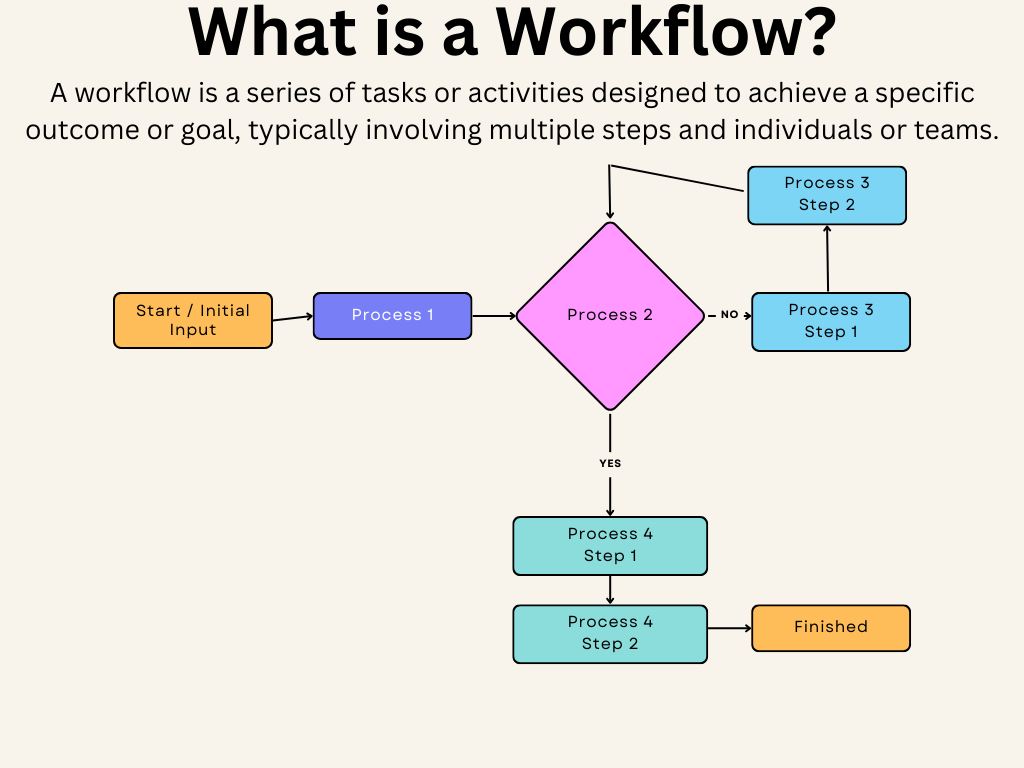
As you develop and map out the process, aim to keep things as simple as possible. Even complex tasks should be free of unnecessary steps, redundancies, and other potential bottlenecks.
Your detailed implementation plan should include:
- Timelines and a list of milestones to guide progress
- Roles and responsibilities of all involved parties
- Details regarding resource allocation and usage
For a deeper dive into everything this step entails, check out our article on workflow documentation.
5. Train Your Employees
You’ll now need to train all relevant employees on the new standardized process.
The first step here is to present and explain the new way to your teams as it pertains to them. Ensure they know exactly what will change — and the positive impact the change will have on their on-the-job experience.
From there, use a combination of training approaches to fully communicate the new process and give your team time to practice working through it. Using training software to provide interactive and media-rich training sessions can help keep employees engaged, motivated, and immersed in the new way of doing things.
6. Implement the New Standardized Process
You’ll now be ready to begin rolling out the new process — ideally in a slow-but-sure manner.
If possible, implement the new process in a controlled, low-risk environment. For high-risk processes, consider using simulated experiences to bridge the gap between training and real-world rollout.
Similarly, a phased approach can help you identify potential issues with the workflow before they cause any major damage. Your top employees and best-performing teams, as appropriate, can act as pilots to help guide company-wide rollout moving forward.
7. Monitor and Improve the Process
As you fully implement the new process, you’ll need to continually make rolling improvements over time.
Again, this involves analyzing employee performance data and stakeholder feedback — along with any observations you make as you manage your team from day to day. This combination of automated and manual data analysis will give you a comprehensive outlook of how the new process is working, and where things could be better.
For small, growing businesses, continuous improvement is the only option.
Process Standardization Best Practices for 2024
Now that we understand the steps involved in process standardization, let’s dig into the key best practices to follow throughout.
1. Showcase the Value and Impact of the Change
As we touched on, it’s crucial that your employees understand why the standardization is happening — and how it will impact them.
One way to do this is to showcase how other teams have fared when making similar changes to their operations. Real-world examples will not just prove that successful standardization is possible, and is always worth doing.
Beyond the surface level benefits like increased productivity and error reduction, focus your employees on the big picture. Show them how standardizing this process will make other parts of their job that much easier — and, in many cases, allow them to accomplish even more without overextending themselves.
2. Engage Stakeholders at All Stages
Everyone involved in the standardization process should, to some degree, be involved in all steps of the process.
There are three key reasons for this:
- For one, gathering valuable input from subject matter experts will help you optimize the new process from all angles — and help you avoid making major mistakes from the start.
- You’ll also get a better idea of what your team is capable of and, in turn, what your training initiatives will need to involve.
- Lastly, you’ll keep them involved and informed throughout development and implementation of the new process. This provides them open opportunities to provide additional feedback as needed — and also keeps them prepared to jump into the new way once rollout begins.
Build Flexibility and Scalability into the Process
Since you’ll inevitably need to make improvements to your standardized workflows in the future, you’ll want to develop the process with this flexibility in mind.
Essentially, this means creating a process that:
- Can easily scale as your company grows, and
- Can be over time without interrupting operations
One effective practice here is to create processes in modular segments that can be easily adjusted or replaced without disrupting the entire system. This allows for quicker adaptations to changes in business operations or external conditions.
It’s also important that your standardized processes allow for flexibility during day-to-day operations as needed. Building much too rigid workflows can cause production to screech to a halt when things go even slightly off-course.
Provide Accessible and Transparent Information
Keeping stakeholders informed and in alignment throughout the standardization process is vital.
And there are two key things you can do to make it happen.
First, ensure all team members can quickly and easily access the information they need to accomplish what they’ve set out to do. This includes documentation related to planning, training, and implementing the new standard process, and other relevant organizational knowledge content.
It’s also important to establish clear channels for communication specifically related to the initiative — and, again, to document important conversations as needed. While simple Slack channels allow for concentrated real-time and asynchronous chat, immersive social intranet channels can lead to the creation of communities of practice around your new standard.
Provide a Supportive Transition
No matter how talented and motivated your employees are, they’ll likely need a fair amount of support when standardizing processes.
To begin with, be sure not to overload them with too many simultaneous or subsequent changes. And definitely don’t get caught in the trap of making change for the sake of change, as this will cause your team to burn out for literally no reason.
Comprehensive training is again a must — as is proper support throughout training and beyond. Consider creating mentorships or other ongoing, cohort-based support systems to provide guidance to employees as they navigate unfamiliar processes.
Prioritize Standardizing Knowledge Management
We spoke earlier about the importance of standardizing your core operations — specifically those that impact your operations most — first and foremost.
Since every business runs on organizational knowledge, we’d argue that knowledge management is the first area you should focus on. In standardizing your KM workflows, you’ll be better able to manage the swath of information and data created in the initiatives to follow.
And, of course, optimizing your approach to knowledge management will lead to major improvements in your operations elsewhere — even before standardization happens.
Wizardshot + Helpjuice: Two Cornerstones of Process Standardization
With the above being said, it’s clear that a way to easily document your processes and knowledge base software are essential to your standardization efforts.
Enter: Helpjuice.
With our knowledge base software, you’ll be able to:
- Create comprehensive process documentation and other helpful resources for team members and stakeholders
- Collaborate with other team members to optimize knowledge content over time
- Analyze usage data to identify knowledge gaps — and uncover new areas to standardize and optimize in turn
Want to get started for free? Sign up for a 14-day trial of Helpjuice today!